放電加工の未来を拓く!最新技術とその可能性を探る
2024/10/28
放電加工は、ものづくりの最前線で最新技術を駆使し続ける重要なプロセスです。本記事では、放電加工の未来を拓く最新技術とその可能性に迫ります。AIやIoTの導入により、加工精度や効率が飛躍的に向上し、環境に優しい製造プロセスが構築されています。また、複雑な形状や微細構造の製造が可能となり、医療機器から航空宇宙産業まで幅広い分野での応用が期待されています。
目次
放電加工の進化最前線AIとIoTがもたらす革新
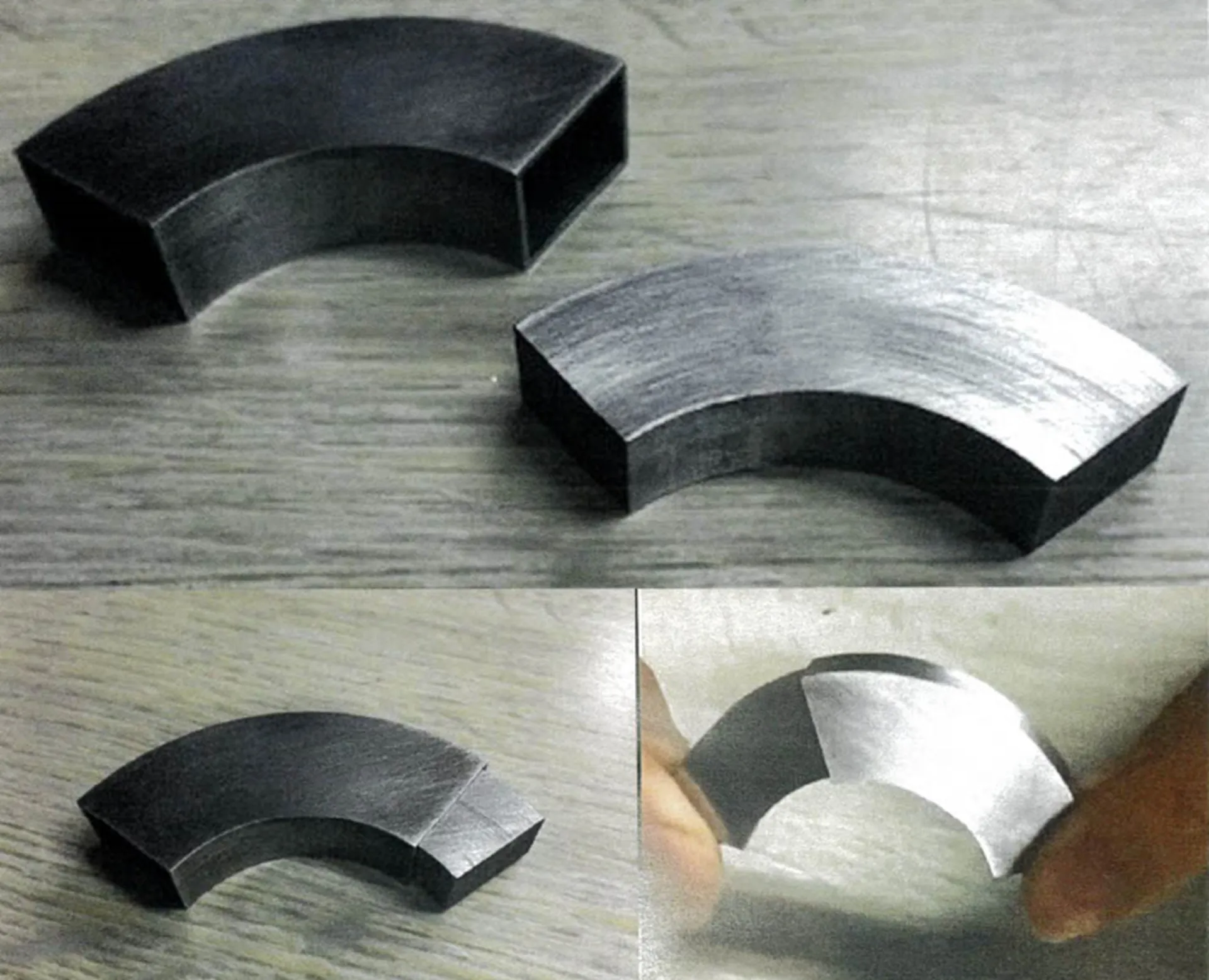
AIが実現する放電加工の新たな精度
放電加工においてAIの導入は、精度の飛躍的な向上をもたらしています。従来の加工方法では実現できなかった微細な調整と高精度な加工が、AIの力を借りて可能になっています。AIは大量の加工データを解析し、リアルタイムで最適な加工パラメータを設定することで、加工中の誤差を最小限に抑えます。この結果、製品の品質向上と同時に加工時間の短縮が実現され、生産効率が大幅に向上します。また、AIは学習機能を持ち、過去のデータをもとに次回の加工をより精度の高いものにすることが可能です。こうした技術の進化は、放電加工の精度を新たな次元へと引き上げ、複雑な形状や微細構造の製造が求められる分野での応用が拡大しています。

IoTとの連携によるリアルタイム制御
放電加工におけるIoTの活用は、加工プロセスのリアルタイム制御を飛躍的に向上させています。IoTデバイスは加工装置に取り付けられ、膨大なデータをリアルタイムで収集し、AIと連携して加工条件を迅速に調整します。これにより、加工中に発生する微細な変動や異常を即座に検知し、常に最適な状態で加工を続行することが可能です。特に、IoTが提供するリアルタイムデータは、加工の中断を最小限に抑えるだけでなく、予防保守にも役立ちます。これにより、機械の稼働率が向上し、長期的なコスト削減にも繋がります。このようにしてIoTは、放電加工の現場に革新をもたらし、より効率的で高精度な製造を支えています。

AIとIoTの相乗効果とその可能性
AIとIoTの相乗効果は、放電加工における技術革新を加速させています。AIは加工中のデータをリアルタイムで解析し、IoTが収集した大量のセンサーデータと組み合わせることで、加工プロセスの精度を飛躍的に向上させます。この連携によって、加工条件の自動調整が可能となり、最適化された効率的な生産プロセスが実現します。たとえば、AIが加工中の微細な誤差を予測し、IoTがその情報をクラウド上で共有することで、全体の生産ラインが一体となって改善に取り組むことができます。このように、AIとIoTの技術が融合することで、これまでの放電加工の概念を大きく変革し、製造の新たな可能性を切り拓いているのです。

データ解析が促進する加工プロセスの最適化
放電加工におけるデータ解析は、プロセスの最適化を促進する重要な要素となっています。加工中に得られる膨大なデータをAIが解析し、各工程における最適な加工条件を導き出します。これにより、微細形状や複雑な構造の加工がより精密に行えるようになります。このプロセスは、特に高精度が求められる医療機器や航空宇宙分野での応用が期待され、品質の向上と生産効率の最大化を可能にします。また、データ解析によるフィードバックループにより、加工の安定性が向上し、トラブルの早期発見も可能となります。これらの取り組みが、放電加工における精度と効率を劇的に進化させ、新たな境地を開拓しているのです。

次世代自動化を支えるスマート技術
次世代自動化を支えるスマート技術は、放電加工の未来を大きく変える可能性を秘めています。特にAIとIoTの進化によって、加工プロセスがより一層スマートに、そして効率的に行われるようになっています。例えば、AIの導入により、機械学習を活用した自動化プログラムが開発され、複雑な形状の部品加工でも高精度な仕上がりが期待できます。また、IoT技術を活用することで、リアルタイムでのデータ収集と分析が可能になり、加工機の状態を常にモニタリングすることで、ダウンタイムの最小化やメンテナンスの最適化が実現されています。このようなスマート技術は、業界全体の生産性向上に寄与するだけでなく、新しいビジネスモデルの創出をも促進しています。これにより、放電加工は次世代の製造業において不可欠な技術としての地位を確立するでしょう。

放電加工におけるデジタル化の未来
放電加工におけるデジタル化は、製造業の未来を形作る重要な要素として注目されています。特に、デジタル技術の活用により、これまで以上に精密で効率的な加工プロセスが可能となり、新しい市場ニーズに対応した製品開発が進んでいます。例えば、CADやCAMソフトウェアの進化により、設計から製造までの一貫したデジタル化が実現され、設計の自由度が向上しています。さらに、デジタルツイン技術を活用すれば、実際の加工現場を仮想空間で再現し、シミュレーションを通じて最適な加工条件を探ることができます。これにより、試行錯誤のプロセスが削減され、製品の開発スピードが大幅に向上しています。デジタル化された放電加工は、環境に配慮した持続可能な製造プロセスの実現にも寄与し、未来の製造業を支える重要な役割を果たすでしょう。
複雑形状の限界を超える放電加工の未来展望

ナノスケール加工が拓く新しい地平
放電加工技術の進化によって、ナノスケールでの精密な加工が可能となり、さまざまな産業に新たな道を開いています。この技術は、ナノメートル単位の正確さを求められる分野で特に有用であり、微細なプロトタイプから量産品まで、幅広い製品の製造に適用されています。例えば、医療分野では、ナノスケール加工が医療機器の表面処理に貢献し、より安全で効果的な医療サービスの提供を可能にしています。また、航空宇宙産業においても、材料の微細な構造を最適化することで、機体の軽量化や燃費効率の向上が期待されています。放電加工の応用範囲は無限であり、今後もさまざまな分野でその可能性が探求され続けるでしょう。

限界を超える微細加工技術の進化
放電加工は、これまでの加工技術の限界を乗り越える可能性を秘めています。従来の技術では実現が難しかった微細で複雑な形状の加工も、今では精密な制御と高度な技術力により可能となっています。特にAIやIoTを用いたリアルタイムの加工条件最適化により、プロセスの効率化と精度向上が進んでいます。これにより、エネルギー消費を抑えつつ高品質な製品の製造が実現できるため、環境負荷の低減にも寄与しています。さらに、放電加工技術は、従来の製造法では対応しきれなかった特定のニーズに応える新たな加工方法を提供しており、未来の産業界における重要な技術基盤となっています。このように、放電加工の技術革新は、限界を打破し続け、ものづくりの新たな時代を切り開いています。

複雑形状に対応する革新的な加工法
複雑な形状を持つ部品の製造において、従来の切削加工では限界がありました。特に、微細で複雑な形状を持つ部品を製造する際には、従来の方法では望ましい精度を保つことが困難です。そこで、放電加工の重要性が増しています。放電加工は、物理的な接触が不要な非接触加工法であり、どのように複雑な形状でも高精度に成形可能です。この革新的な技術により、設計の自由度が大幅に向上し、デザイナーやエンジニアに新たな可能性を提供しています。

3Dプリンティングとの融合で広がる可能性
近年、3Dプリンティング技術と放電加工の融合が新たな製造ソリューションとして注目されています。3Dプリンターは自由な形状創造を可能にする一方で、表面仕上げや内部構造の微調整には限界がある場合があります。ここで放電加工が活躍します。この二つの技術を組み合わせることで、3Dプリントされた部品に対して、さらに高精度な加工や表面仕上げが可能となります。これにより、航空宇宙分野や医療分野などでの応用が益々広がり、多様なニーズに応えることができるのです。
医療機器における放電加工技術の新しい可能性

医療分野での高精度加工の重要性
医療分野では、高精度な部品加工が求められるケースが多く、放電加工技術はそのニーズに応える重要な手段となっています。特にマイクロスケールの精密部品の製造において、放電加工はその優れた特性を発揮します。たとえば、カテーテルやインプラントなど、人体に直接関わる医療機器の製造では、微細な寸法精度が患者の安全性に直結します。このため、放電加工技術の導入が進んでおり、その精度の高さは他の加工方法にはない利点を提供します。また、この技術は加工中の熱の影響を最小限に抑えるため、材料の物理特性を保持するのにも役立ちます。AIやIoTを活用した加工プロセスの最適化により、その精度がさらに向上し、医療分野における放電加工の重要性はますます増しています。

微細構造が可能にする医療機器の革新
微細構造を実現する放電加工技術は、医療機器の革新に貢献しています。たとえば、微細な電極やセンサーを持つデバイスの開発が進行中で、これにより一層精密な診断や治療が可能になります。放電加工は、複雑な形状を持つ部品の製造を可能とし、その結果、デザインの自由度が大幅に向上します。また、微細な構造は、生体組織との適合性を向上させ、医療機器の信頼性を高める要素ともなります。高精度な加工により、部品の表面粗さを抑えることができ、これが生体内での摩擦を減少させる効果を持ちます。このような技術革新は、医療現場での実用性を高め、患者の負担軽減や治療効果の向上に直結するため、多くの企業が積極的に研究開発を進めています。

機器の安全性を高める放電加工技術
放電加工技術は、その高精度な加工能力によって、医療機器の安全性を大幅に向上させる手段として注目されています。特に心臓ペースメーカーや人工関節など、人体に直接接触する機器では、安全性が最重視されます。放電加工は、摩擦や腐食から部品を保護するための微細な表面処理を可能にし、これにより機器の長期的な信頼性を確保します。また、特定の電極材料を使用することで、放電加工は医療機器の導電性や絶縁性を最適化し、誤作動のリスクを低減します。さらに、この技術は既存の部品に対する補修や改良にも活用されており、医療現場での機器の寿命を延ばす役割を果たしています。放電加工による安全性向上は、医療機器の品質向上とともに、患者の安心感を高める要素としてますます重要視されています。

生体適合性を考慮した材料加工
放電加工は、生体適合性を考慮した材料加工においても、その技術的優位性を発揮しています。特に、インプラントや人工臓器の表面処理において、放電加工は生体組織との親和性を高めるために不可欠です。この技術により、材料表面の粗さを精密に調整することが可能になり、組織の接着性を向上させます。その結果、異物反応を抑制し、人体への負担を軽減することができます。また、放電加工は生体適合性に優れた新素材の加工にも対応可能であり、その応用範囲は医療分野にとどまらず、幅広い分野で期待されています。さらに、放電加工技術の進化により、従来の加工方法では難しかった微細構造の製造が可能となり、より高度な生体適合性を実現するための道が開かれています。このように、放電加工は医療技術の進化において、欠かせない役割を果たしています。
航空宇宙産業を支える放電加工の最新技術

高性能部品を実現する放電加工の役割
放電加工は、素材を腐食させて形状を削り出す非接触加工法として、高性能部品の製造に不可欠な技術です。特に、金属の硬度や耐久性を維持しつつ、精密な形状を実現できることから、電子機器や自動車部品の製造に多く利用されています。AIによる加工条件の最適化や、IoT技術を活用したリアルタイムの状態監視により、従来よりも高い精度と効率での加工が可能となっています。これにより、設計の自由度が広がり、新しい製品のイノベーションが加速しています。

軽量化を促進する新技術の導入
放電加工技術は、軽量化を求める現代の製造業においても重要な役割を果たしています。特に、複雑な形状を持つ部品や微細な構造を持つ部品の製造が可能であるため、材料の無駄を最小限に抑えつつ、必要な強度を確保することができます。さらに、3Dプリンティング技術と組み合わせることで、従来の加工方法では難しかった軽量かつ高強度な構造を実現しています。これにより、輸送機器や航空宇宙産業における燃費向上やコスト削減に寄与しており、持続可能な製造プロセスへの貢献が期待されています。

極限環境に耐える加工精度の追求
極限環境における放電加工の加工精度は、特に航空宇宙産業や医療機器などの分野で不可欠な要素です。従来の加工技術では困難とされていた高度な精度を実現するために、最新の放電加工技術はAIや機械学習を駆使して、ミクロン単位の精密加工を可能にしています。これにより、過酷な温度変化や圧力条件においても高い耐性を持つ部品の製造が行えるようになり、製品の信頼性が向上します。このような技術革新は、製造工程における時間短縮とコスト削減をもたらし、企業が競争力を持つ上での大きなアドバンテージとなっています。さらに、放電加工の応用範囲が広がることで、次世代の高性能材料の開発にも貢献し、新たな製品設計の可能性を開拓しています。

航空宇宙産業における新材料対応
航空宇宙産業では常に新しい材料の導入が求められており、放電加工はその対応力を高める技術として注目されています。新素材の開発は、軽量化や高強度化といった性能向上を目指す一方で、加工の難易度が増すことが多いです。放電加工は、無接触で加工できるため、脆い材料や硬度の高い材料にも対応可能です。この特性を生かし、新素材に対するダメージを最小限に抑えつつ、精密な形状を造り出すことができます。特に、複雑な形状や微細構造を持つ部品においては、そのメリットが顕著に現れます。結果として、航空宇宙分野での革新的な設計自由度が広がり、より高性能で信頼性の高い製品を生産することが可能になっています。
環境に優しい放電加工持続可能な製造プロセスへ

資源効率を高める新しい加工法
放電加工は、材料の無駄を最小限に抑える加工方法として注目されています。従来の方法では、切削や削り取りによって大量の廃材が発生することが一般的でした。しかし、放電加工では、電極と加工物の間で放電を発生させて材料を加工するため、必要な箇所だけを精密に加工することが可能です。このため、材料の使用効率が向上し、資源の浪費を抑えることができます。さらに、AIによる加工プロセスの最適化が進んでおり、材料の選定や加工パラメータのリアルタイム調整が可能になっています。これにより、資源効率のさらなる向上が期待されており、環境負荷の低減に貢献しています。

エネルギー消費削減のための技術革新
放電加工におけるエネルギー消費の削減は、技術革新によって大きな進展を遂げています。新しい電源技術の導入により、加工時の電力消費が大幅に削減されています。例えば、最新のパルス制御技術を使った電源ユニットは、必要な電力だけを効率的に供給することが可能です。また、加工プロセス全体をモニタリングし、無駄なエネルギー消費を防ぐIoT技術の活用も進んでいます。これにより、加工の精度を維持しながらエネルギーを節約できるようになりました。さらに、AIを活用した自動化システムは、加工条件の最適化をリアルタイムで行うことができ、これもエネルギー消費の抑制に寄与しています。このような技術革新は、持続可能な製造プロセスの実現に向けた重要なステップです。

廃棄物ゼロを目指すクリーン製造
放電加工技術の進化は、製造過程における廃棄物削減に大きく寄与しています。従来の製造プロセスでは、削りくずや廃液などの廃棄物が多く発生していましたが、最新の放電加工技術を駆使することで、これらの廃棄物を大幅に削減することが可能です。また、精度の高い加工を行うことで、素材の無駄を減らし、必要最小限の材料で製品を製造することができます。さらに、廃棄物をゼロに近づけるための新しい取り組みとして、AIを活用したプロセス管理や最適化が進んでいます。これにより、加工時のエネルギー消費も最適化され、環境への負荷がさらに軽減されます。これらの技術革新により、廃棄物ゼロを目指すクリーンな製造プロセスが次世代のものづくりにおいて重要な役割を果たすことが期待されています。

リサイクル可能な材料の活用
放電加工技術は、リサイクル可能な材料の活用を促進する上で、非常に重要な役割を果たしています。特に、再生可能な金属や合金の加工が可能な点で、持続可能な製造の未来を築く鍵となっています。例えば、新素材の開発においては、放電加工を用いてリサイクルされた材料を高精度で加工することが可能であり、これにより新しい製品として再利用される機会が増加します。このようなリサイクル可能な材料の活用は、資源の無駄を減らし、環境負荷を軽減するだけでなく、コスト削減にも繋がります。さらに、放電加工技術の進展により、複雑な形状や微細な構造を持つリサイクル材料の加工が可能となり、製品の品質向上にも貢献しています。このように、リサイクル可能な材料の活用を通じて、持続可能な社会の実現に寄与する放電加工技術は、今後ますますその重要性を増していくことでしょう。

持続可能性を考慮した設計指針
放電加工では、持続可能性を考慮した設計指針が重要な役割を果たしています。設計段階から環境負荷を最小限に抑えるための取り組みが求められています。具体的には、再生可能な材料の選定やリサイクル可能な部品の使用が推奨されます。また、放電加工プロセスにおいても、エネルギー消費を抑えつつ高精度な加工を維持することが求められます。AIによる加工条件の最適化や、IoTを活用したプロセス管理により、無駄を排除し、資源を最大限に活用することが可能です。こうした取り組みにより、持続可能な未来に向けた製造の在り方が大きく変わりつつあり、放電加工はその先駆けとなっています。

環境規制に対応する未来の製造プロセス
環境規制の厳格化に伴い、放電加工の分野でも未来志向の製造プロセスが求められています。放電加工技術は、微細加工が可能であるため、無駄を最小限に抑えたクリーンな製造が可能です。さらに、最新の技術革新により、環境基準をクリアするための新しい加工法が続々と開発されています。例えば、従来の方法に比べてエネルギー消費が大幅に削減できるプロセスの導入や、廃棄物を出さないクローズドループシステムの実装が進められています。こうした未来の製造プロセスは、持続可能な製造業の実現に貢献するだけでなく、企業にとっても競争力を生む要因となり得ます。本記事を通じて、放電加工の未来とその可能性を理解し、次世代の製造業に期待を寄せていただければ幸いです。
精度と効率を両立する放電加工の技術革新

精密加工を実現する最新の技術
放電加工技術は、近年の技術革新によって精密加工の新たな領域を切り開いています。その鍵となるのはAIやIoTの導入であり、これにより加工条件のリアルタイム最適化が可能になっています。この技術は、従来の手法では達成困難であった微細構造や複雑形状の高精度加工を実現し、医療機器や航空宇宙産業など、幅広い分野での応用が進められています。特に、ナノスケールでの加工が求められる場合には、AIと組み合わせた高度な制御システムが必要とされ、これにより製品の品質が大幅に向上します。また、放電加工は熱変形の影響を最小化するための冷却システムの最適化も重要であり、これがさらなる精度向上に寄与しています。

効率化を図るプロセス自動化の進展
放電加工におけるプロセス自動化は、製造業全体の効率化に大きく貢献しています。特にAI技術の導入によって、加工プロセスのリアルタイムモニタリングとフィードバック制御が可能となり、加工の精度と効率が飛躍的に向上しています。このような自動化技術は、複雑な形状や微細加工が求められる部品の製造においても、その効果を発揮します。また、IoT技術を活用することで、データの収集と分析が行われ、不要なプロセスの削減やエネルギー効率の改善が図られます。これにより、環境に優しい製造プロセスが構築され、持続可能な製造業の実現に向けた取り組みが進んでいます。さらに、自動化技術の進展は、労働力不足の解消や作業者の負担軽減にも寄与しており、製造業界全体の生産性向上が期待されています。

精度向上に寄与する新素材の利用
放電加工における精度向上の鍵を握るのは新素材の利用です。近年、放電加工においては、従来の金属素材に代わる新しい素材が次々と開発されています。特に、ナノ材料や高強度セラミックスなどの新素材は、より高い加工精度を実現するために重要な役割を果たしています。これらの新素材は、微細な加工を可能にするだけでなく、工具の摩耗を低減し、加工効率を高めることができます。また、新素材の導入によって、より複雑な形状を持つ部品の製造も可能となり、航空宇宙や医療といった高度な技術が要求される分野での応用が広がっています。これにより、放電加工の可能性はますます拡大し、業界全体の技術進化に貢献しています。

作業効率を高める人材育成と技術支援
放電加工の効率化を図る上で、人材育成と技術支援の重要性はますます増しています。最新技術を効果的に活用するためには、技術者のスキルアップが不可欠です。企業は、技術者が新しい加工技術や設備を迅速に習得できるよう、定期的な研修や技術セミナーを実施しています。また、AIやIoTを活用した技術支援ツールの導入により、リアルタイムでの加工データ分析が可能となり、技術者がより的確な判断を下せる環境が整いつつあります。これにより、作業効率が向上し、製造現場での生産性が大幅にアップすることが期待されています。人材育成と技術支援の充実は、今後の放電加工の競争力を高めるための重要な要素となっており、業界全体での取り組みが進行しています。
放電加工とデジタル技術の融合がもたらす未来

デジタルトランスフォーメーションの影響
放電加工の分野におけるデジタルトランスフォーメーションは、製造プロセスの変革をもたらしています。具体的には、加工機のデジタル化が進み、プロセスの可視化やリアルタイムでのモニタリングが可能となっています。これにより、加工精度や効率が向上し、従来の方法では難しかった微細加工も実現可能となりました。また、デジタル技術の導入により、加工条件の最適化やトラブルの未然防止も行われています。AIやIoTとの連携によって、加工機の稼働状況をリアルタイムで把握し、必要なメンテナンスを適切なタイミングで実施することが可能となります。これにより、設備の稼働率が向上し、無駄を削減することができます。さらに、デジタルトランスフォーメーションは、放電加工のプロセスを一層効率的かつ環境に優しいものに変える可能性を秘めています。

仮想現実を用いた加工シミュレーション
放電加工における仮想現実(VR)技術の導入は、加工シミュレーションの手法を大きく変えるものです。VRを用いることで、物理的な加工機を使わずに仮想空間でのプロセスをシミュレーションすることが可能となり、加工条件の最適化を事前に行うことができます。この手法により、素材の無駄を減らし、時間とコストの削減を実現します。また、VR技術はオペレーターの技術習得にも寄与し、安全な環境でのトレーニングが可能です。加工シミュレーションを通じて、熟練した技術者がいない場合でも、高精度な加工を実行することができます。さらに、リアルタイムでのフィードバックを通じて、プロセスの改善点を迅速に把握し、実際の加工に反映させることが可能です。

サイバー空間でのプロセス最適化
放電加工におけるプロセス最適化は、サイバー空間での技術革新により新たなステージに進化しています。デジタルツイン技術を活用することで、物理的な環境を仮想空間に再現し、加工プロセスのシミュレーションをリアルタイムで行うことが可能となりました。これにより、加工の最適化を試行錯誤せずに実現し、時間とリソースの節約が可能です。さらに、サイバー空間ではAIが加工条件を分析し、最適なパラメータを提案することで、効率と精度を飛躍的に向上させます。例えば、異なる材質や形状に合わせた加工条件の最適化を、高速かつ的確に行うことが可能です。これにより、放電加工がより柔軟かつ高度なプロセスとして進化し、多様な製造ニーズに応えることができるのです。

データ駆動型の意思決定プロセス
放電加工の世界では、データ駆動型の意思決定プロセスがますます重要視されています。大量の加工データを収集し、AI技術を用いて詳細な分析を行うことで、より確実な判断を下すことが可能になります。このアプローチにより、従来は経験や勘に頼っていた部分が、客観的なデータに基づく科学的なプロセスへと進化します。特に、加工精度や効率の向上が求められる現代において、データ駆動型のアプローチは競争力を維持するための鍵といえます。さらに、このプロセスは持続的な改善を可能にし、製品の品質を向上させるだけでなく、生産コストの削減にも寄与します。データの収集・分析を通じて、各ステップの改善点を明らかにし、それをフィードバックとして反映することで、放電加工の未来をより明るいものとすることができるでしょう。

クラウド技術による設備管理の変革
クラウド技術の進展は、放電加工設備の管理に新たな風を吹き込んでいます。これにより、従来のオンプレミス型の設備管理から脱却し、クラウドベースでのデータ管理が可能となりました。この変革は、リアルタイムでのデータアクセスと分析を容易にし、設備の稼働状況やメンテナンスの必要性を即座に把握することを可能にします。また、クラウド技術を活用することで、複数の設備を遠隔から効率的に監視・管理でき、運用コストの削減と稼働効率の向上を同時に実現します。放電加工業界においても、クラウドによる設備管理の効果的な活用は、競争力のある製造プロセスを支える重要な要素となっています。今後もクラウド技術を駆使した設備管理の進化が期待され、業界全体の生産性を底上げすることでしょう。

高度なセンサー技術で実現するリアルタイム分析
高度なセンサー技術の導入は、放電加工においてリアルタイムでのデータ分析を可能にし、プロセスの最適化に貢献しています。センサーが加工中の微細な変化を感知し、そのデータをリアルタイムで分析することで、加工精度を向上させ、異常の早期発見を実現しています。このプロセスは、加工品質の一貫性を保ちながら、効率的な生産をサポートします。さらに、センサー技術は環境の変化や新しい材料への柔軟な対応を可能にし、多様化する市場のニーズに応える力を提供します。放電加工の未来を見据えた技術革新は、これらのセンサーによるリアルタイム分析の進化によって、より高い精度と信頼性を持つ加工プロセスを実現します。これにより、製造業界における新たな可能性が広がることを期待せざるを得ません。次回も、さらなる技術革新とその展望に注目していきますので、どうぞご期待ください。
微細構造製造の可能性を拓く放電加工テクノロジー

微細加工が可能にする製品革新
放電加工の進化により、微細加工技術が劇的に向上しています。この技術は、特に製品の小型化や高機能化に寄与し、従来の加工方法では難しかった複雑な形状や精密な部品の製造を可能にしています。例えば、医療機器や航空宇宙産業において、微細加工は不可欠となっており、さらなる製品革新の可能性を広げています。このように、放電加工は現代のものづくりを支える基盤技術として、その重要性を一層高めています。微細加工による製品の高精度化と軽量化は、競争力のある製品開発において欠かせない要素となり、製品設計の自由度を増すことで新たなアイデアを具現化するチャンスを提供しています。

新しい製品設計を実現する技術の進化
放電加工技術の進化は、新しい製品設計の可能性を大きく広げています。AIやIoTの導入により、加工プロセスはより精密かつ効率的になり、新たなデザインの実現が可能となっています。この技術的進化は、設計者が従来の制約を超えた創造的なアプローチを採用することを可能にし、より革新的な製品の開発を促進します。例えば、自動車産業では、軽量かつ安全性の高い部品設計が求められており、放電加工技術はその実現に大いに貢献しています。今後も放電加工を駆使した技術革新が、様々な産業分野において新しい製品設計を実現し、さらなる進化をもたらすことが期待されます。

高精度要求に応える放電加工能力
放電加工の高精度能力は、製造業界における競争力を強化する要因の一つです。特に、複雑な形状や細かなディテールが要求される部品の製造において、その重要性はますます高まっています。最新の放電加工技術は、ナノ秒単位のパルス制御を実現し、加工精度を飛躍的に向上させることが可能です。さらに、AIを活用した加工条件の最適化によって、リアルタイムで精度を保ちながら効率的な生産が行えます。こうした技術革新により、医療機器や精密機械部品など、高精度が求められる分野での製品開発を加速させています。これにより、放電加工は高精度要求に応えるための不可欠な技術として、今後さらに注目されていくでしょう。

微細構造がもたらす新産業分野の開拓
放電加工技術の進化は、微細構造の製造を可能にし、新たな産業分野の開拓を促進しています。特に、マイクロ放電加工技術の発展により、従来の機械加工では難しかった微細なパターンや形状の製造が可能となりました。この技術は、バイオテクノロジーやナノテクノロジーといった新興分野での応用が期待されており、今後の産業の発展に大きく寄与することが予想されています。さらに、微細加工技術は、半導体や電子機器の製造においても重要な役割を果たしており、より高性能なデバイスの開発を支えています。こうした新産業分野の開拓により、放電加工はさらなる市場拡大と技術革新の可能性を秘めているといえるでしょう。

次世代材料との相乗効果を生む加工法
放電加工技術は、次世代材料と組み合わせることでその可能性を最大限に引き出します。特に、航空宇宙や自動車産業で使用される耐熱性や耐久性に優れた新素材に対して、放電加工は非常に有効です。これにより、高精度な加工が要求される複雑な部品でも、品質を犠牲にすることなく効率的に製造が可能となります。また、次世代材料との相乗効果により、放電加工の利便性と精度が更に向上し、製造業界全体に新しい革新をもたらします。これらの進歩は、製品の性能向上だけでなく、新しい設計理念の実現をも支援し、未来の製造プロセスにおける重要な要素となるでしょう。こうした技術進化により、放電加工はさらに広範な産業分野での応用が期待され、未来の製造業をリードする存在となります。

競争優位を確保するための技術革新
放電加工技術の発展は、企業が競争優位を維持するための鍵となっています。最新の放電加工技術は、製品の精度と品質を高めると同時に、加工時間の短縮とコスト削減を可能にします。特に、AIとIoTの導入により、加工プロセスの最適化は飛躍的に進化し、製造工程全体の効率化が図られます。これにより、市場の変化に迅速に適応できるだけでなく、顧客の多様なニーズにも応えることが可能です。さらに、技術革新は製品開発のスピードを加速し、新しいビジネスチャンスを創出します。本記事を通じて、放電加工技術がもたらす未来の可能性を探ることで、業界の未来を形作る革新の重要性を再確認できました。次回も新たな技術の動向を追い続けていきますので、ぜひご期待ください。